Clorox Atlanta Plants Have Zero Tolerance — for Waste
By Steve Clarke, Environmental & Sustainability Manager
At Clorox, the zero-waste-to-landfill sites keep coming.
Our Atlanta Main and Atlanta West Home Care plants are the latest to meet our zero-waste-to-landfill (ZWtL) criteria. This brings the total number of Clorox certified ZWtL locations to 15, exceeding the company’s 2020 ZWtL goal by 50%.
This is a great way to end the 2020 goal period and sets a good pace to meet our IGNITE Strategy goal that 100% of our plants worldwide be ZWtL by 2025 (where infrastructure allows).
Each new site must overcome unique challenges and find local solutions to achieve true ZWtL status, and our Atlanta plants were no exception.
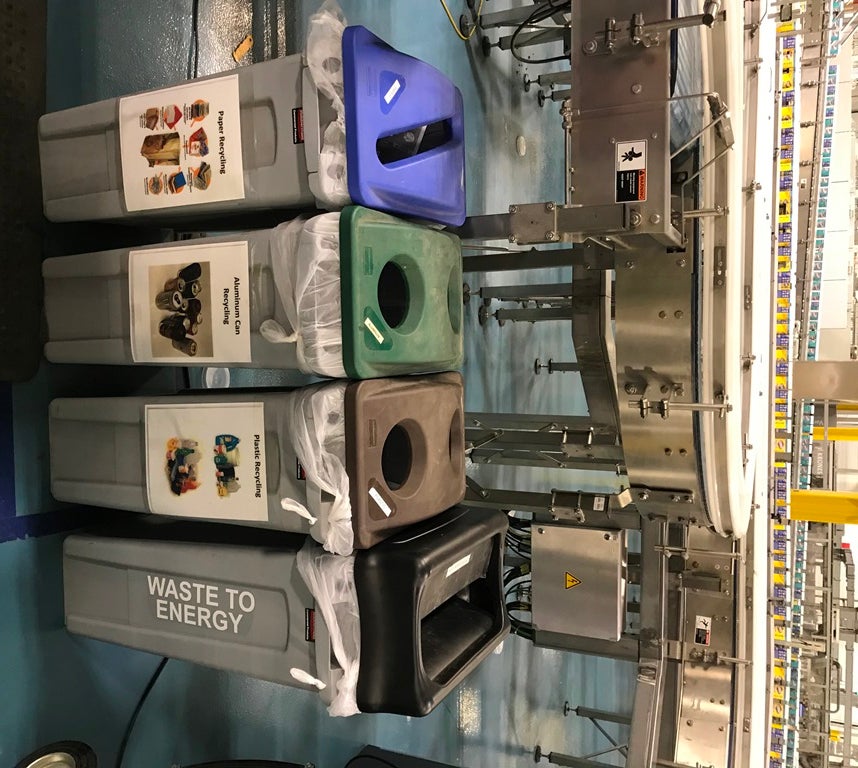
Waste diversion bins on the plant floor
Atlanta Main
Atlanta Main has maintained an impressive recycling/reuse rate of greater than 95% since 2015.
The team achieved this by setting up a robust recycling program, adding balers for plastic and cardboard and implementing a process to reuse rejected plastic bottles by regrinding the plastic to mold new bottles.
“We’ve had very good systems in place to recycle material in the plant for several years,” said Linn Stoller – Facilities Manager.
Eric Eckstrum, Environmental Coordinator, added, “Plant employees were all very engaged in recycling. However, our biggest challenge was to find a solution for the plant’s project waste.”
So Linn and Eric brought this challenge to Mike Kelly, the plant engineering manager.
“We decided to meet with contractors, corporate engineers and our waste vendor to see if we could work out a solution,” Mike recalled.
From that collaboration, the team developed new processes to segregate material for reuse or recycling when equipment is purchased or decommissioned. Our contractors also agreed to break down non-recyclable material that has energy value so it can be sent to a waste-to-energy plant.
“Finding a solution for the project waste was the last piece of the puzzle the plant needed to be certified ZWtL,” said Eric.
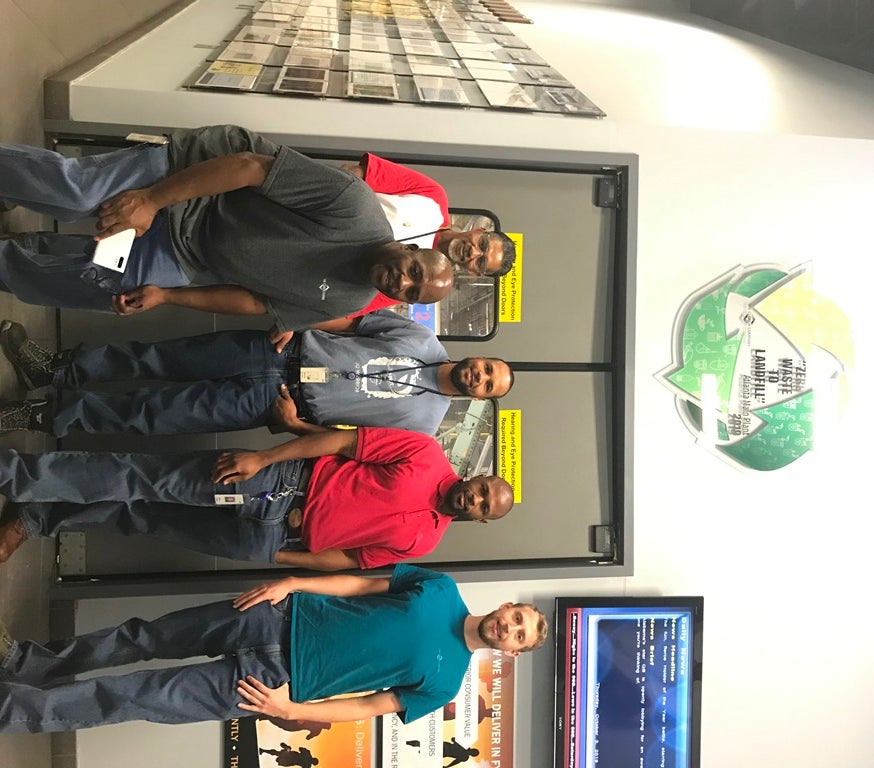
The Atlanta Main eco team
Atlanta West
As a brand new facility in 2018, Atlanta West had a different set of challenges.
“We were able to include recycling, reuse and waste-minimization procedures as part of the plant’s overall design and start-up, so passing the corporate audit was not an issue,” said Marc Benson – plant manager. “Our big concern was that we were creating more scrap substrate waste than anticipated.”
According to Gary Hyde – distribution manager, “Almost 65% of our waste stream was from scrap substrate, and we couldn’t find anyone to take it.”
The plant’s first step was to reduce that volume by improving various processes. Then, after a couple of years’ search, they found a company that could take the material and shred it for a filler.
“This allowed the plant to improve its recycling/reuse rate to 91%,” said Terrel Dean – environmental coordinator.
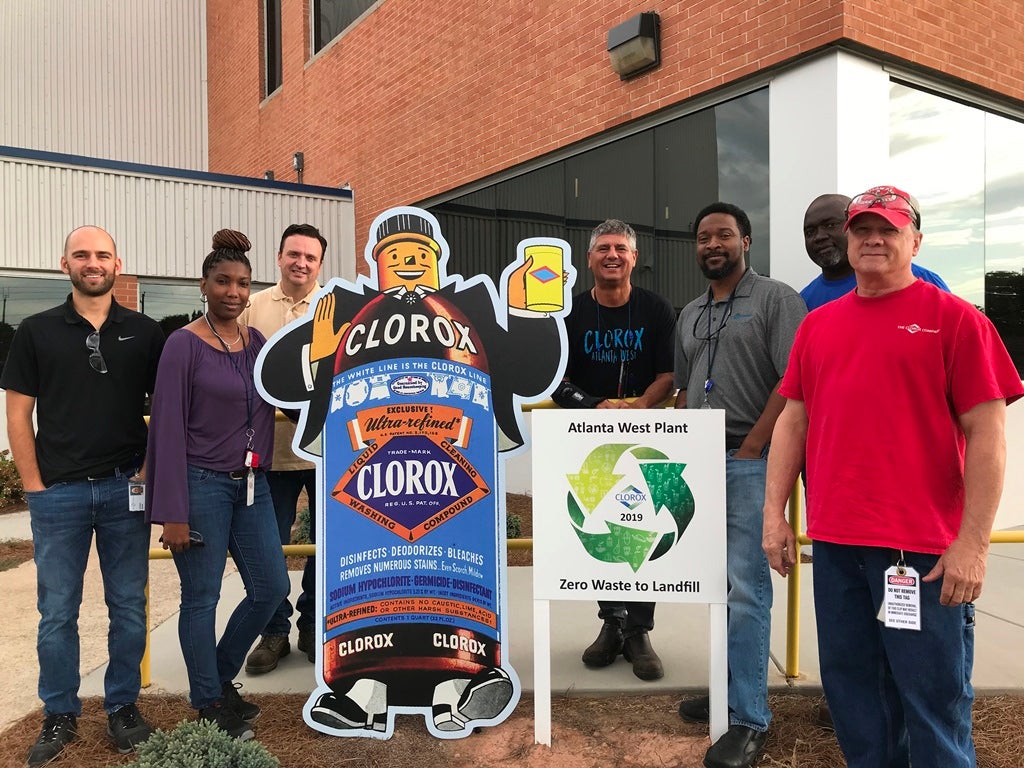
The Atlanta West eco team
Working together to win
The teams at Atlanta Main and Atlanta West really stepped up, with broad engagement and significant improvements in their recycling, sustainably and waste minimization efforts.
Most importantly, both plants have been working hard to reduce their overall waste volumes in order to achieve and maintain zero-waste-to-landfill status.
Related:
Glad Global Facilities Go Zero Waste
Glad R&D Cracks Formula for Zero Waste to Landfill
Glad Amherst Journeys to Zero Waste to Landfill
Clorox Mexico Dumps Landfills for Good
Glad® Rogers Plant: The Hero of Zero