Keeping our environmental commitments during the pandemic production surge
By Steve Clarke, Environmental & Sustainability Manager and Morgan Hale, Manufacturing Leadership Development Program
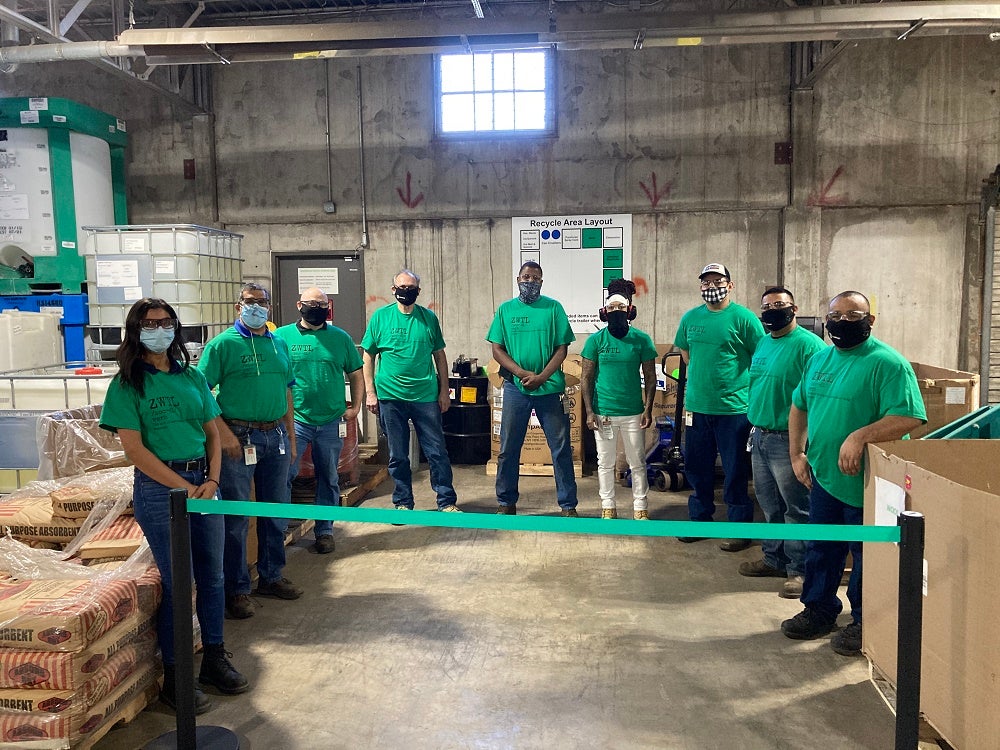
Houston’s Trash Panda’s: Nisha Mistry, Arnold Mallett, Joe Rutter, Randi Hughes, Vincent Warren, Domonique O’veal, Mark Garza, David Rodriguez, Robert Balleza, and Jesse Parmain (not pictured).
Our bleach plant in Houston, Texas, wasn’t about to let a global pandemic derail its zero-waste journey.
After years of work, the site met Clorox’s zero-waste-to-landfill (ZWtL) criteria in December 2020. The milestone is all the more noteworthy because it was reached at a time when the plant was producing record amounts of bleach — under new safety protocols — to meet surging demand from COVID-19.
Houston’s path to zero
The path to zero started with a dumpster dive, this one in 2018. The results were sobering. “Honestly, we weren’t sure if we could do it — or if zero waste was even possible for out site,” recalled Arnold Mallett, Houston plant manager.
The Houston plant faced a number of unique challenges to become ZWtL. Changes in the recycling market meant there were several waste streams with hard-to-recycle items. And the closest waste to energy (WtE) plant was over 500 miles away in Tulsa, Oklahoma, which is a long haul for waste.
The team in Houston slowly chipped away at each obstacle, starting with improving its recycling.
“We were baling our scrap bottles in a large baler, but we didn’t know what to do with the small amount of stretch wrap we had,” said Randi Hughes, Environmental Coordinator. “Vincent Warren found a small, affordable compactor nearby that was ideal for baling small volumes, which makes it easier to sell to a recycling company.”
One problem down.
Randi and the plant’s Eco team found other innovative solutions for their waste streams. They segregated hard plastics and set up puncturing systems to drain aerosol cans so the metal could be recycled. The plant worked with vendors to return totes and cardboard slip sheets for reuse. The team even found a company to repurpose used conveyor belts.
“Slowly, our recycling and reuse rates improved from 85% to over 90%,” remarked Joseph Rutter, Plant Engineering Manager. “We were closing in on our ZWtL goal, but we still had to find a waste-to-energy outlet and pass the audit.”
In late 2019, opportunity came knocking. Our corporate recycling partner found that a new waste-to-energy processing facility was opening in the Houston area in 2020. Coincidently, it was the same company that Burt’s Bees uses, so Clorox already had a working relationship with them. Houston sent its first load to the local waste-to-energy location in the fall of 2020, generating both environmental and cost savings since we no longer had to truck the material 500 miles to be recycled.
Conducting environmental site checks during COVID
Finally, all that remained was the final audit by our Global Safety & Environmental (GSE) team. Everything was in place, only the plant was in overdrive to meet unprecedented demand due to the pandemic. Nevertheless, the local Eco team remained committed to achieving ZWtL status despite the increased production hours and material flowing in and out of Houston.
Since it wasn’t safe to travel, the team used technology like “smart glasses” for a July 2020 pre-audit. The GSE team, based in Kennesaw, Georgia, identified areas that needed better visibility, organization and handling. Houston was almost there.
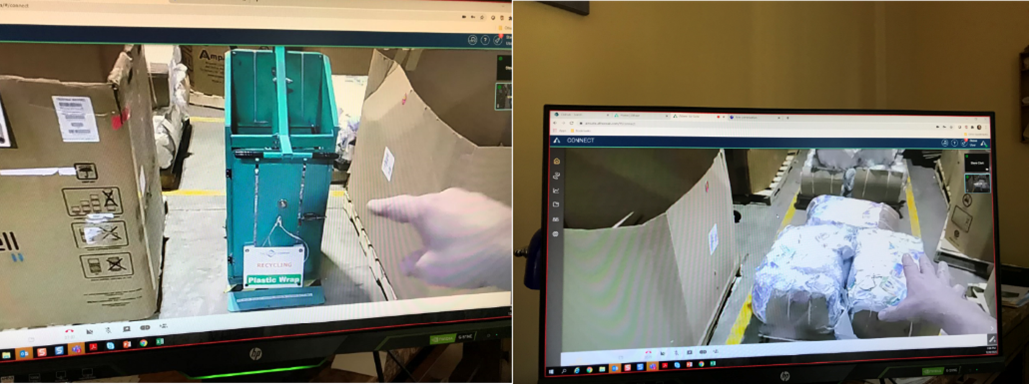
The zero-waste audit at Clorox’s Houston plant was conducted virtually using “smart glasses” and chat. The audit inspected waste containers throughout the plant.
So the Houston plant rolled up its proverbial sleeves, rebranded the Eco team as the “Trash Pandas” and stepped up its recycling game. The newly inspired team made some major improvements: A new recycling center housed a multitude of materials, all clearly labeled and properly organized. A new training program bolstered employees’ existing knowledge and set the stage for new habits. Inspections became routine to ensure everything was in its place and processed the right way.
The plant passed its December audit with flying colors. The audit team in Kennesaw — still remote — saw major changes from July to December, and also saw that new ways of working required by the pandemic needn’t distract or detract from our commitment to sustainability and achieving important environmental goals.
Learn more about our IGNITE ESG goals, including our goal to make 100% of our global plants zero-waste-to-landfill by 2025 and all facilities by 2030.