Clorox Evolves Safety Score
By Jamie Owen — Global Safety, Health, Environment, & Sustainability
The Clorox Company is evolving how it measures safety to include more emphasis on leading metrics.
We believe this will help us further improve our already world-class safety program.
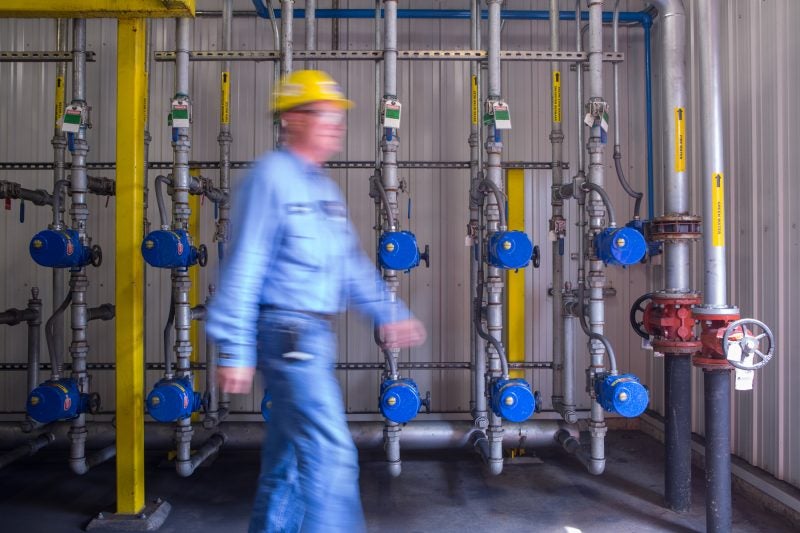
Safety is a core Clorox value. A Kingsford plant in Belle, Missouri.
We ended fiscal year 2017 with a gold safety rating. Our recordable incident rate was 0.60, better than our world-class stretch goal of 0.75 This reflects our corporate commitment to workplace safety — a core value for Clorox.
Better still, we finished the year with three fewer reportable injuries than we had the previous year. While not statistically significant, any reduction in people getting hurt is good news.
Always improving
All Clorox plants are graded on World Class Organization (WCO) Scorecards. Safety is one of those.
Every year, we look for ways to improve our already excellent safety program.
For fiscal year 17, that meant a shift away from discussing only numbers and outcomes to discussing the human efforts behind those numbers.
We focused on the safety process and doubled down on the daily commitment from every employee that a truly safe workplace culture demands. This included training and knowledge sharing, which we will continue.
For fiscal year 2018, we are evolving and expanding the safety metrics we report internally.
While we will continue to track the recordable incident rate, starting now, the WCO safety scorecard will be tabulated almost exclusively on leading metrics. We will weigh heavily things like the number of near-miss incidents that are investigated and whether a plant performs regular area audits and an analysis of findings.
Focusing on leading safety metrics (how to identify potential safety issues before they occur) rather than reporting trailing metrics (after-the-fact numbers) will help create an even stronger safety program.
Clorox will still celebrate safety milestones, but we’re going to really emphasize and recognize the work that goes into reaching such milestones.
Expanding Human & Organizational Performance (HOP)
The safety metrics we have now put into place reflect our expansion of Human & Organizational Performance (HOP) philosophy.
This approach emphasizes the need to learn from incidents that occur and to reduce the potential risk for severe incidents in the future.
All of our Kingsford sites as well as the Burt’s Bees and Fairfield, Calif., cleaning plants have been through the HOP training. Additional plants are scheduled for training this fiscal year.
These changes and a stronger emphasis on learning support our growth culture and safety as a core Clorox value.